When to use a Soft Start versus a Variable Speed Drive
A soft starter is, as you would expect, a device which ensures a soft starting of a motor. A Soft Start has different characteristics to the other starting methods. It has thyristors in the main circuit, and the motor voltage is regulated with a printed circuit board. The softstarter makes use of the fact that when the motor voltage is low during start, the starting current and starting torque is also low.
Advantages
Soft starters are based on semiconductors. Via a power circuit and a control circuit, these semi-conductors reduce the initial motor voltage.
This results in lower motor torque.
During the starting process, the soft starter gradually increases the motor voltage, thereby allowing the motor to accelerate the load to rated speed without causing high torque or current peaks.
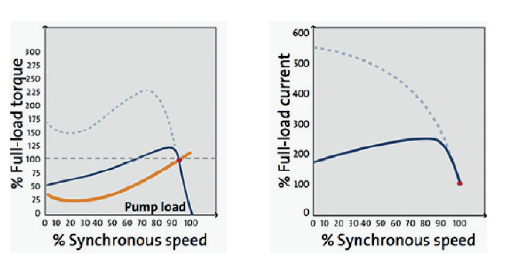
Soft starters can also be used to control how processes are stopped. Soft starters are less expensive than frequency converters.
Soft Starter Drawbacks
They do, however, share the same problem as frequency converters: they may inject harmonic currents into the system, and this can disrupt other processes.
The starting method also supplies a reduced voltage to the motor during start-up.
The soft starter starts up the motor at reduced voltage, and the voltage is then ramped up to its full value. The voltage is reduced in the soft starter via phase angle. In connection with this starting method current pulses will not occur. Run-up time and locked-rotor current (starting current) can be set.
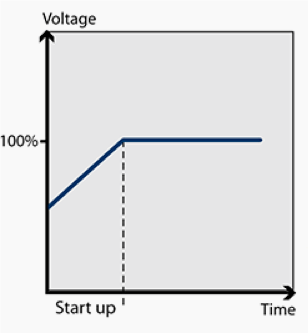
Variable Speed Drive Starting
Frequency converters are designed for continuous feeding of motors, but they can also be used for start-up only.
The frequency converter is sometimes also called VSD (Variable Speed Drive), VFD (Variable Frequency Drive) or simply Drives, which is probably the most common name.
The drive consists primarily of two parts, one which converts AC (50 or 60 Hz) to DC and the second part which converts the DC back to AC, but now with a variable frequency of 0-250 Hz. As the speed of the motor depends on the frequency this makes it possible to control the speed of the motor by changing the output frequency from the drive and this is a big advantage if there is a need for speed regulation during a continuous run.
As stated above, in many applications a drive is still only used for starting and stopping the motor, despite the fact that there is no need for speed regulation during a normal run. Of course this will create a need for much more expensive starting equipment than necessary.
By controlling the frequency, the rated motor torque is available at a low speed and the starting current is low, between 0.5 and 1.0 times the rated motor current, maximum 1.5 x In.
Another available feature is softstop, which is very useful, for example when stopping pumps where the problem is water hammering in the pipe systems at direct stop. The softstop function is also useful when stopping conveyor belts from transporting fragile material that can be damaged when the belts stop too quickly.
It is very common to install a filter together with the drive in order to reduce the levels of emission and harmonics generated.
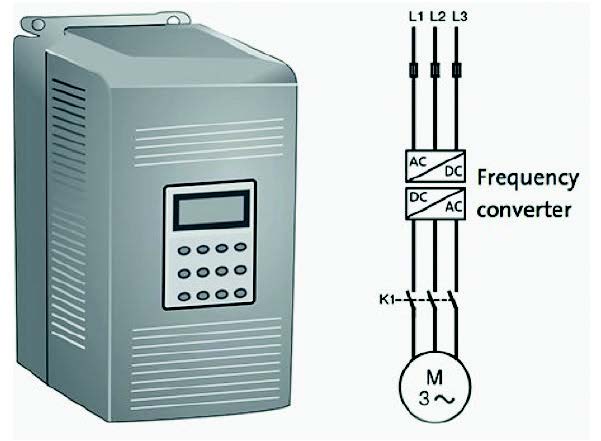
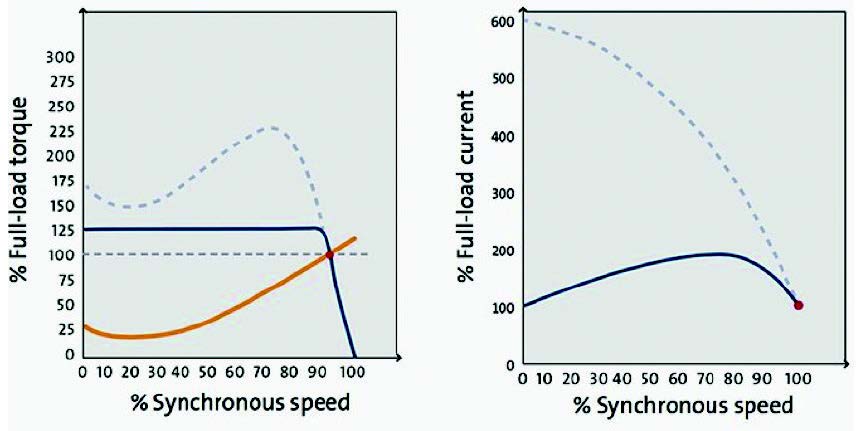
Drawbacks
Even so, frequency converters are still more expensive than soft starters in most cases; and like soft starters, they also inject harmonic currents into the network.
Although manufacturers’ catalogues try to make it easy as possible, there are many variables associated with the selection and rating of the optimum electric motor and AC converter for a Variable Speed Drive (VSD) application. In many cases, it requires considerable experience to get the selection right.
The reason why it is difficult is because there is always an engineering trade-off between following:
• The need to build in a margin of safety into the selection procedure
• The need to keep the initial cost to a minimum, by selecting the optimum type and size of motor and converter for each application.
Checklist
The following checklist covers most of the factors that need to be considered:
• The nature of the application
• Maximum torque and power requirements and how these change with speed
• Starting torque requirements
• The speed range – minimum and maximum speed
• Acceleration and deceleration requirements (Is braking necessary??)
• Compatibility with the mains supply voltage
• Environmental conditions where the converter and motor are required to operate, ambient temperature, altitude, humidity, water, chemicals, dust, etc.
• Ventilation and cooling for the converter and motor
• Direction (uni-directional or bi-directional)
• Accuracy of the speed control
• Dynamic response (speed and torque response requirements)
• Speed regulation requirements with changes in load, temperature, supply voltage
• The duty cycle, including the number of starts and stops per hour
• Overall power factor of the drive system and its effect on the mains supply
• EMI and harmonics in the mains power supply, in the motor and motor cable
• Are EMI filter required??
• Earthing, shielding and surge protection requirements
• Torque pulsations in the rotor shaft
• Control method – manual, automatic, analog, digital, communications
• Control and communications interfaces required for the plant control system
• Indications required
• Reliability requirements, is a dedicated standby unit required
• Protection features, in-built and external features required
• Power and control cable requirements
• Parameter settings, local or remote programming
• Maintenance, spares and repair considerations
• Cost of the alternative systems, taking into consideration the capital cost, performance advantages, energy savings, efficiency or process improvements.
• Noise due to the harmonics in the motor
• Mechanical resonance at certain motor speed